

The rate of penetration general equation is optimized for effective functions at each data point. A model is developed for this purpose using actual field data collected through modern well monitoring and data recording systems, which will be predicting the rate of drilling penetration as a function of available parameters. An extensive literature survey on drilling optimization was conducted for this research study. A Statistical method namely multiple linear regression technique is used for the drilling optimization methodology. Real time optimization of drilling parameters during drilling operations aims to optimize weight on bit, bit rotation speed for obtaining maximum drilling rate as well as minimizing the drilling cost. A look ahead, discussing other magnetic sensor technologies that can potentially be used in the oil/gas industry is presented, and what is still needed in order deploy them in the field is also addressed. Therefore, this paper aims to serve as an opportunity for researchers to truly understand how magnetic sensors can be used in a downhole environment and to provide fertile ground for research and development in this area. Research into magnetic sensors for oil/gas drilling has not been explored by researchers to the same extent as other applications, such as biomedical, magnetic storage and automotive/aerospace applications. These magnetic sensors play a critical role in drilling wells safely, accurately and efficiently into a target reservoir zone by providing directional data of the well and acquiring information about the surrounding geological formations. In this paper we present a review of the application of two types of magnetic sensors-fluxgate magnetometers and nuclear magnetic resonance (NMR) sensors-in the oil/gas industry. The proposed control algorithm selects the drilling parameters in order to minimize the time of the drilling process and the deviation from the target trajectory. The real-time control is updated at regular distance intervals. The control commands include the angular velocity and torque of each of the 4 motors. In this work a real-time control and optimization of the QMDH is simulated and extensively evaluated under various drilling scenarios.

A QMDH uses four drilling bits, independently controlled by 4 downhole motors. Quad Motor Drilling Heads (QMDH) were recently proposed to achieve smooth and intuitive directional drilling. HDD reduces environmental impact to accomplish the installation process and minimizes the drilling time and cost. Different trenchless installation techniques have been developed over the years but Horizontal Directional Drilling (HDD) technique is commonly used for pipelines installation beneath buildings, forests, or lakes without excavation or at least minimum digging due to its steering capability.
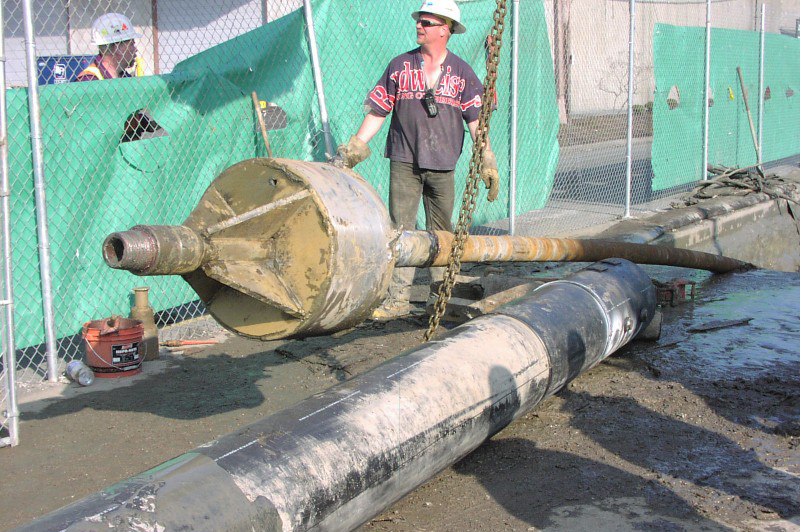
Trenchless technology gained more popularity than open trench due to its economic and environmental factors, it facilitates the installation, replacement, or rehabilitation of underground utility systems with minimum disruption of the surface. Over the past 25 years trenchless technology has flourished in many pipeline installation applications as water industry, sanitary sewer, and natural gas pipeline industry.
